Article classificationArticle
UPDATED GFX/XTS SYSTEM TO CATER FOR MORE INDUSTRIES, MORE APPLICATIONS AND MORE CUSTOMERS
Since its inception over 5 years ago, HepcoMotion’s GFX, the high-end mechanical framework for the Beckhoff XTS drive system, has gone from strength-to-strength.
Absorbing the considerable process forces that act on the movers and workpieces, GFX provides the transport path and mechanically guides the movers along the motor modules at the defined speed with great precision. The XTS drive allows movers to be controlled individually; as a result, work processes of different duration can be combined, product and process changes are possible and workstations can be added or removed as needed. GFX/XTS has quickly been adopted as the system of choice for higher duty XTS applications where motion profile and long term durability requirements are particularly demanding. Responding to customer demands, HepcoMotion and Beckhoff have continued to collaborate and develop the GFX/XTS system to cater for more applications, more industries and more customers.
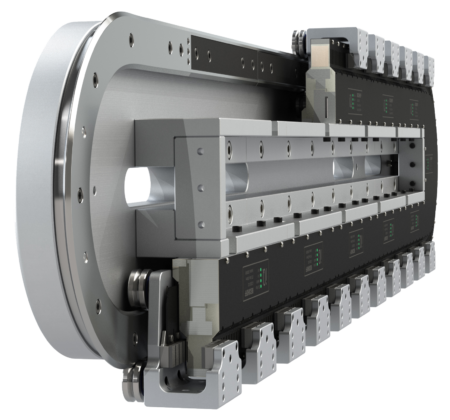
The GFX/XTS system has four new developments: Hi-Drive, a solution for heavier applications; Agile, for lighter loads; the Hygienic System for operation in wet environments and the Track Management System, an ingenious track switching solution.
Hi-Drive
A standard GFX/XTS system has a load capacity of up to a few Kg; at most up to 10kg if you pair movers together. For many applications, this is more than sufficient but there are some circumstances where a higher load is needed. For example, with an automotive sub-assembly line, mass is being added at each work station, resulting in a heavy mass at the end of the production line. The system therefore needs to provide speed and accuracy, but at higher loads than has previously been possible on a system such as the GFX/XTS. Until now.
As a direct response to market demand, HepcoMotion and Beckhoff have developed the new GFX Hi-Drive. Hi-Drive provides a more robust mover, and also increases drive force through the use of larger magnets. The result is a system that can move heavier payloads with performance that isn’t compromised by the available linear drive force. Specified for overall payloads (product and tooling and process load combined) of up to 20kg per mover, Hi-Drive is capable of a maximum velocity of 4m/s and acceleration of 40m/s².
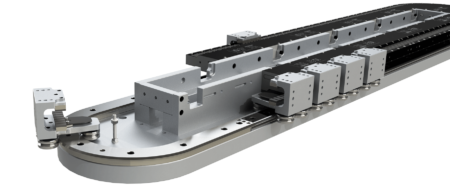
Offering the same accuracy and repeatability as the standard GFX/XTS system, Hi-Drive can handle twice the capacity. Moreover, when programmed through TwinCAT with a specific ‘pairing protocol’ XTS coding from Beckhoff, 2 movers can be paired in a stacked, mechanically linked configuration, giving a single drive axis up to 40kg. The 10 pole mover provides over 200N of drive force, the 7 pole offering around 150N.
Hi-Drive movers incorporate a 7 & 10 pole magnet array, enabling the XTS to generate greater drive forces or the same drive forces with reduced heat generation in the motor modules.
Agile
For every application that requires a higher load, there is another application that simply requires more speed; this is where the new GFX Agile comes in. GFX Agile has been designed to be light and fast. The bearings are smaller with a lower mass, which allows the movers to accelerate and decelerate to and from top speeds quicker.
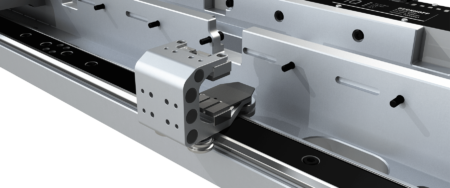
The transit time is therefore significantly less, allowing a higher throughput. Designed for overall payloads (product and tooling combined) of less than 250g, with little or no process loading, GFX agile is capable of a maximum velocity of 6m/s and acceleration in excess of 200m/s² when programmed through TwinCAT with specific ‘unlocked’ XTS coding from Beckhoff.
GFX Agile uses less energy and therefore generates less heat in the modules, allowing more throughput to thermally limited applications where our conventional movers demand greater energy for the required acceleration or velocity profile capacity of the XTS drive systems. Overall system lengths can also be reduced to achieve the same throughput, saving valuable space. Aimed at lightweight applications focussed on maximising throughput, GFX Agile is ideally suited to the packaging or filling of small confectionary or pharmaceutical products for example.
Track Management System
The next development is the Track Management System (TMS); a clever design that facilitates the transition of movers between GFX systems, connecting two systems seamlessly. During continuous operation, movers can be switched out of the circuit or even moved onto secondary circuits thanks to TMS. This enables movers to be removed for maintenance reasons, to allow for system re-configuration or for the movement of movers between systems to accommodate extra processes. There are many potential uses for TMS and its ability to switch during high speed operation enables throughput to be maximised. The precision ballscrew driven transfer slide section can achieve cycle times as quick as 0.4 seconds to sub-micron repeatability.
Optimising space is another core advantage of TMS. The footprint remains the same but production can be doubled by having two production lines running in parallel, vertically aligned, one above the other. For applications looking to maximise throughput this can be very advantageous. TMS is proving very popular in applications such as Electric Vehicle battery production. Not only is this system space saving but it also maintains the product in a single orientation; advantageous in EV battery production.
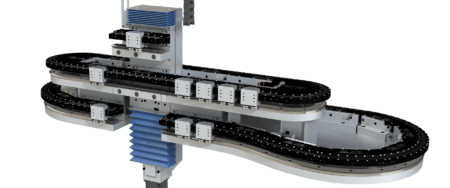
Hygienic Design
Finally, the last development to introduce is the GFX Hygienic Design, a variant of the GFX track system that is suitable for use with the Beckhoff “HD” hygienic design XTS motors and magnets. Opening up a wide spectrum of new applications, primarily in food and pharmaceutical industries and for processing and filling liquids, the GFX Hygienic Design is expected to be well received.
Two versions of the system are available to suit differing customer needs; cleandown and washdown.
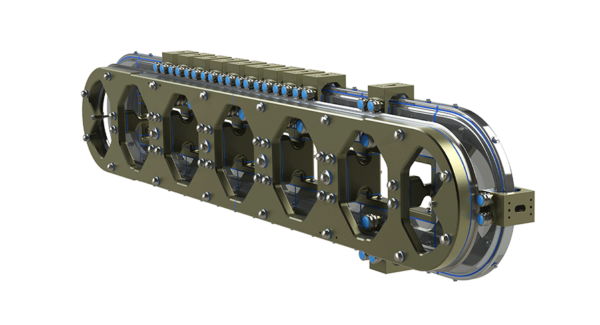
Cleandown
Suitable for wet cleaning, this system uses a structure that is very similar to a standard GFX, but modified with special mover body and motor mounting hardware to fit the HD (Hygienic Design) motors. Designed to be used in pharmaceutical, food and other processes where the system requires wet cleaning with benign liquids to remove surface contamination.
Washdown
Designed for cleaning in place (CIP) operations that include foaming agents, hot washing and pressure washing. The construction allows complete access to all surfaces, pooling traps are removed, joints between all components are sealed and the bearings are protected against lubricant egress with a solid cover and labyrinth seals. All fasteners are sealed and designed to minimize pooling traps and ease cleaning processes.
The new Hi-Drive is available immediately. Hygienic, Agile and TMS are at beta stage. For more information, contact us at sales@hepcomotion.com