Article classificationArticle
HEPCOMOTION IS PLAYING A KEY ROLE IN A NOTORIOUSLY HARSH SLATE CUTTING AND PROCESSING APPLICATION HD
The ability to run without lubrication, in a harsh environment, with a high duty cycle were the performance demands placed on linear motion expert HepcoMotion for a challenging slate cutting and processing application.
Spanish-based machine builders Carpintería Metálica Hermaca S.A.U produce specialist machinery to cut and process slates. Slate turns into dust when cut; there is, therefore, an excessive amount of dust particles in this application. This type of environmental condition can be particularly challenging for a linear motion product – if particles of dirt or dust ingress the system, it can cause mechanical damage. This is why Hermaca searched for an alternative option.
Two parts of the machine required a new solution; a heavy duty actuator to lift the slates and a guidance system for a pick and place application that moves the slates from one position to another. For both of these parts, Hermaca turned to linear motion expert HepcoMotion to specify.
For the horizontal pick and place system, Hepco’s core GV3 linear guide is used to move the slate plates from one position to another. Each carriage is carrying a load of 10kg, and covering 15,000 cycles per day. GV3 is a superior V-based linear motion range designed to serve a diverse range of automation and linear applications. GV3 is ideally suited to this harsh environment thanks to its V guide technology.

Hepco’s V guide system has a unique wiping action that expels debris, making it perform particularly well in harsh environments such as this. The outer diameter of the bearing travels at a faster speed than the inner diameter. The difference in speed causes particles nearer the centre to move outwards to the periphery, and to be expelled. Due to the geometry of the slide and bearing interface, debris is expelled to the outer diameter of the bearing in a spiral motion, away from the running surface. The self-cleaning action has resulted in GV3 working in this environment for…
… more than 15 months with a duty cycle of 23,000 pieces per day, compared to the previous guides which needed changing every 3-4 months.
A further challenge in this environment is that due to the high volume of dust, lubrication is not an option, as any lubrication would cause the dust particles to stick together and build up on the slide. Not many linear slides are able to run dry – most require lubrication to prevent wear of the slide, however Hepco’s V guide technology can confidently run without any lubrication. The V bearings are supplied without lubricators or cap wipers, a key requirement not only for this application, but also for many food, medical and scientific applications.
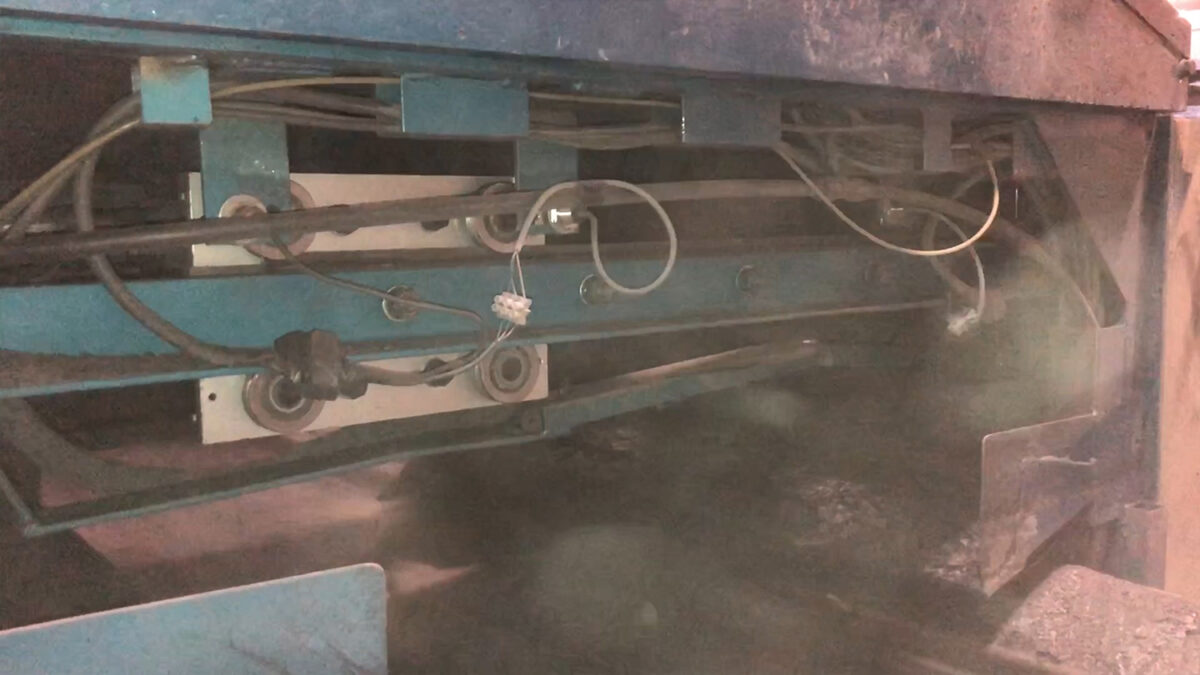
For the vertical lifting of the slate, Hepco’s HDCS heavy duty ball screw actuator is used with bellow covers to protect the actuator from the harsh and dusty environment. The vertical loads of 350kg and the demanding cycle of lifting 23,000 pieces per day requires a heavy duty actuator such as this. The application is typically operational for 8 hours a day, although this increases to 16 hours a days when necessary. The HDCS is proving very reliable and durable – only the internal ball screws need to be replaced every 2 years. The HD slides and bearings are working for 5 or 6 years before needing to be replaced – a big improvement.
The longevity of Hepco’s product in such a notoriously harsh environment has reduced downtime and costs, resulting in increased output. For example, lost production due to downtime has reduced by four times thanks to the GV3 guides only needing to be changed every 15 months, and the HDCS system lasting even longer.
The customer has been using Hepco V guides for many years and is very satisfied with the result.