Article classificationArticle
X Z GANTRY SYSTEM FOR AUTOMOTIVE ASSEMBLY HDS2 system
When a German manufacturer wanted to improve the performance of their XZ gantry system to achieve a longer service life with little to no maintenance, they were faced with a limited number of possibilities.
The previous gantries fitted two linear systems in parallel with mounting to a home made structure. Clearly time savings needed to be made in the assembly process. The task in question was to pick and place car rooftops at various positions over a 15m travel prior to an assembly process.
Solution
A single Heavy Duty beam HB25 with V slides set parallel on the beam was supplied, with a rack cut into one of the slides saving on the need to set a separate rack. A common X carriage was customised to enable the customer to use their existing Z axis arrangement.

Scope of supply
HB25 beam x 16.1m complete with CHSS25NK R3 rack cut vee slide x 16m plus CHSS25NK plain vee slide x 16m mounted. Carriage, rack driven version AURD9535 with 95 mm diameter vee bearings and cap wipers. Fitted gearbox ready for Servo motor attachment.
Result
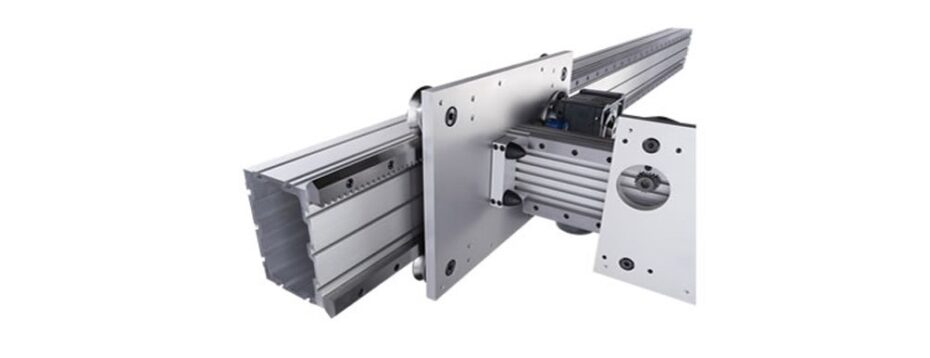
An easy to install system that saves considerably on assembly time, built in parallelism is supplied already set. The low maintenance requirement is satisfied by the fitting of bearing cap wipers fitted with grease. The rack is lubricated by a canister set to distribute a measured amount of lubricant. A simple example showing the use of the standard HDS2 system allowing customising to accomodate an existing customers choice of Z axis.