Article classificationArticle
MULTI-HEAD DRILLING MACHINE HDS Heavy duty sliding system
The task: design an automated multi-head drilling machine to drill 112 holes in aluminum sheets, 126 inches in length, that are used in the manufacturing of semi-tractor trailers.
Currently CH Engineering’s customer manually drills the holes which is very labor intensive. With the business steadily improving, the customer could not build trailers fast enough.
The drilling machine drills successive rows of 112 holes in 126 inch aluminum sheets which operates in one or two eight hour shifts per day. With the possibility of 4 or 5 drilling heads operating at the same time, the drill carriage provides 300 lbs. of downward load and a net upward force of 1,000 lbs. when drilling.
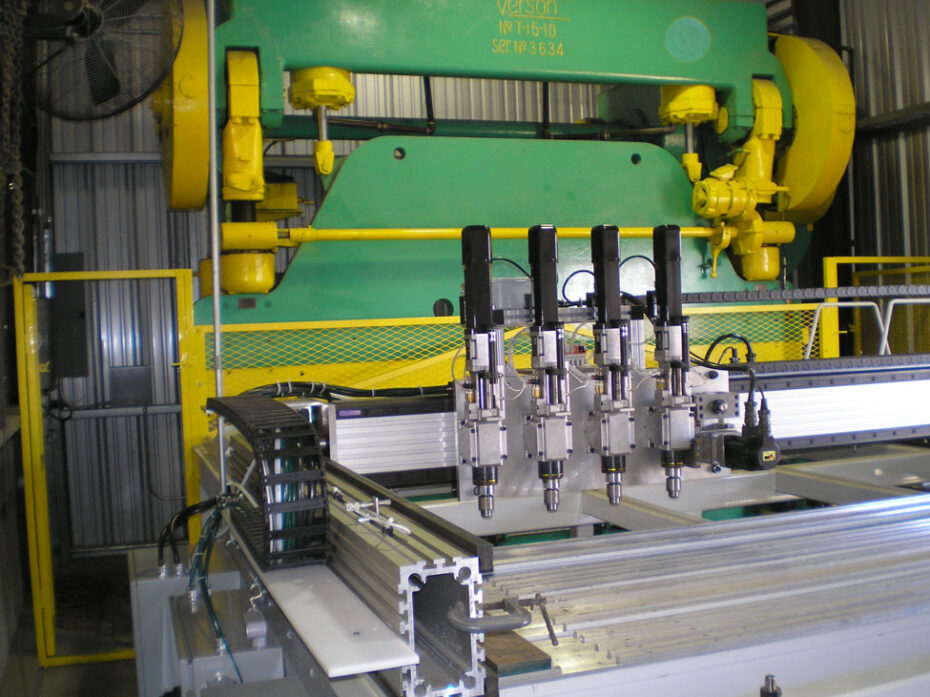
Solution
CH Engineering chose the Hepco HDS Heavy Duty Slide System because it provided the rigidity needed to drill the holes accurately across the large sheets. Roller bearing blocks were selected for the drill carriage assembly to provide better load capability and absorb the every day pounding or usage. The X axis is powered by a servo motor with drive shafts. Shaft-type pinions are mounted to each side of the drive shafts enabling it to drive on the geared tracks.
Scope of Supply
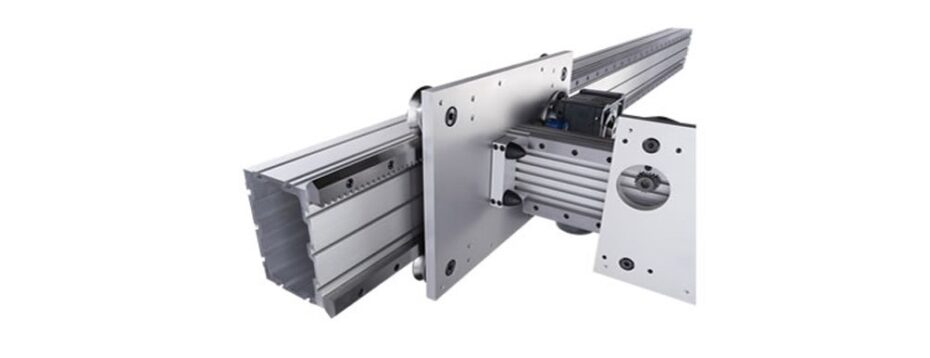
HDS Heavy Duty Slide System
– HB25 beam
– Single edge “V” slides
– Flat tracks
– Roller bearing blocks
– Pinions
Result
Reinforcing rods were installed on the 12 foot Y axis which resulted in approximately 40% higher rigidity and deflection of less than .002 inches across the entire Y axis. Since the shop floor is not level, the customer was delighted with these results. The Y axis is also servo motor driven to the geared track. The entire machine, secured to the shop floor, is mounted to a machined base to provide the needed accuracy.